El diagrama de Ishikawa, también conocido como diagrama de causa y efecto o espina de pescado, es una herramienta poderosa que te ayuda a identificar las causas raíz de un problema. A menudo se utiliza en proyectos de mejora continua, ya que permite analizar los factores que influyen en un problema de manera visual y estructurada. En este tutorial, te guiaré paso a paso para crear un diagrama de Ishikawa y descubrir cómo puedes aplicarlo a situaciones reales.
¿Cómo crear un diagrama de Ishikawa?
- Define el problema: Coloca el problema principal en la “cabeza” del pez.
- Identifica las categorías principales: Las espinas grandes corresponden a factores clave como el Método, Material, Mano de obra, Máquinas, Entorno y Medición.
- Desglosa las causas: Añade las posibles causas a cada categoría. Es importante ser específico y preguntarse varias veces «¿por qué?» para llegar a la raíz del problema. Si no estás seguro/a de a qué categoría corresponde la causa que tienes en mente, no te preocupes, lo importante es que todas las causas estén registradas en el diagrama, más que en que rama se encuentran.
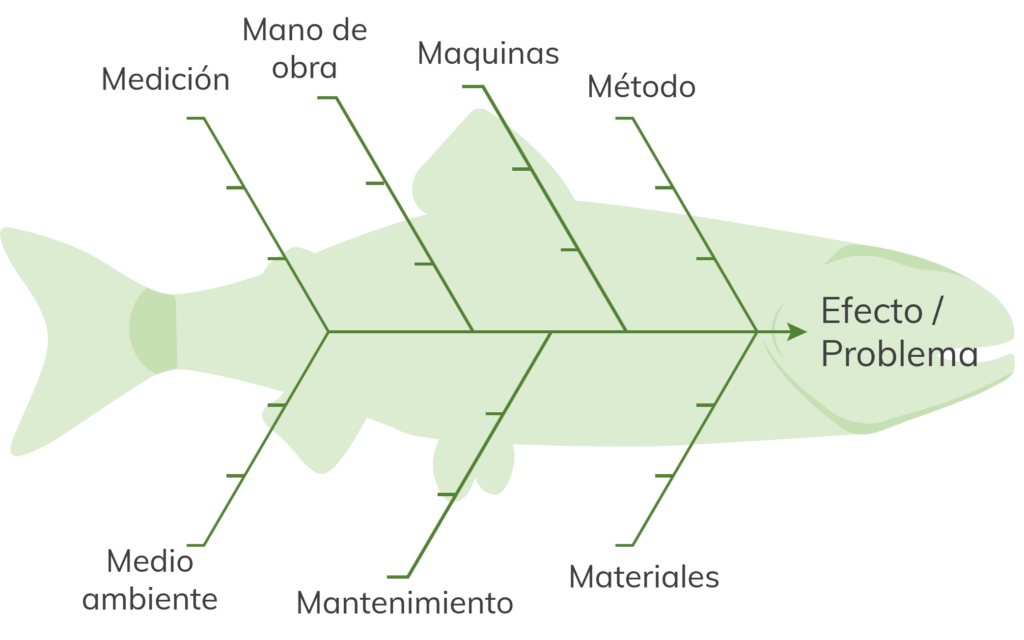
Ejemplos prácticos de uso del diagrama de Ishikawa:
EJEMPLO 1:
Problema central: Alta tasa de defectos en las costuras de una línea de producción textil
1. Método
- Falta de estandarización en los procesos: Los operarios no siguen un procedimiento único para coser, lo que genera inconsistencias en las costuras.
- Instrucciones poco claras: Los manuales o guías para los operarios no están actualizados o son confusos, lo que lleva a errores en la ejecución.
- Tiempos de ciclo mal definidos: No hay una programación clara del tiempo que cada operario debe dedicar a cada tarea, lo que lleva a prisas y fallos.
2. Mano de obra
- Falta de formación adecuada: Los operarios no han recibido la capacitación adecuada sobre el manejo de las máquinas o los procesos de costura específicos.
- Rotación alta de personal: La constante entrada de nuevos empleados significa que siempre hay personal menos experimentado que comete más errores.
- Falta de supervisión: Los supervisores no revisan de manera continua el trabajo de los operarios, lo que permite que los defectos pasen desapercibidos.
3. Material
- Hilo de baja calidad: El hilo utilizado se rompe con facilidad o no se adapta bien al tipo de tela, lo que genera costuras débiles.
- Tela defectuosa: Algunas partidas de tela vienen con imperfecciones que son difíciles de manejar, lo que afecta la calidad de las costuras.
- Variabilidad en las materias primas: Diferentes lotes de tela y hilo tienen características ligeramente distintas, lo que afecta la uniformidad del producto final.
4. Máquina
- Mantenimiento insuficiente: Las máquinas de coser no reciben el mantenimiento adecuado, lo que provoca fallos frecuentes y afecta la calidad de las costuras.
- Equipos desajustados: Las máquinas no están bien calibradas, lo que produce costuras desiguales o con tensión incorrecta.
- Falta de máquinas especializadas: El equipo utilizado no está optimizado para el tipo específico de costura requerido, lo que genera más errores.
5. Entorno
- Condiciones inadecuadas en la planta: Factores como la iluminación deficiente o un espacio de trabajo desordenado afectan la concentración y el rendimiento de los operarios.
- Ruido excesivo: Un entorno ruidoso puede generar distracciones, lo que aumenta la probabilidad de errores.
- Temperatura o humedad descontroladas: Condiciones ambientales como la humedad pueden afectar tanto las máquinas como los materiales, generando defectos en las costuras.
6. Medición
- Herramientas de medición inexactas: Las reglas o calibradores utilizados para medir las piezas de tela no son precisos, lo que lleva a errores en el tamaño y ajuste de las costuras.
- Falta de control de calidad intermedio: No se realizan suficientes verificaciones de calidad durante el proceso, por lo que los defectos no se detectan hasta que ya es demasiado tarde.
- Sistemas de control mal diseñados: Los indicadores de calidad utilizados no reflejan correctamente los problemas que están ocurriendo en la línea de producción.
Estos ejemplos para cada una de las espinas del diagrama de Ishikawa te proporcionan una visión completa de los posibles factores que podrían estar afectando la calidad de las costuras en la línea de producción textil. Usando esta estructura, puedes investigar a fondo cada una de estas causas y tomar acciones correctivas efectivas.
EJEMPLO 2:
Problema central: Contaminación cruzada en productos alimenticios (Industria alimentaria)
1. Método
- Procedimientos de limpieza insuficientes: El protocolo de limpieza entre el uso de equipos para diferentes alimentos no se sigue rigurosamente.
- Manipulación incorrecta de los alimentos: Los empleados no separan adecuadamente los productos crudos y cocidos, aumentando el riesgo de contaminación.
- Almacenamiento inadecuado: Los alimentos no se almacenan de acuerdo a su categoría o nivel de riesgo, lo que facilita el contacto entre ingredientes potencialmente contaminantes.
2. Mano de obra
- Falta de formación en seguridad alimentaria: Los empleados no conocen bien los procedimientos de manipulación segura y las normativas sobre higiene.
- Errores humanos: Distracciones o mala ejecución de los procedimientos causan errores que permiten la contaminación cruzada.
- Descuido en el uso de equipo de protección: Los empleados no utilizan guantes, delantales o redes para el cabello de manera correcta, facilitando la contaminación.
3. Material
- Ingredientes contaminados: Las materias primas ya vienen con contaminación, afectando la seguridad del producto final.
- Embalaje defectuoso: Los empaques no son herméticos o están rotos, lo que expone los alimentos a posibles contaminantes.
- Equipos no aptos para alimentos: El uso de materiales que no cumplen con los estándares de calidad para el contacto con alimentos, lo que puede liberar toxinas.
4. Máquina
- Equipos mal higienizados: Las máquinas no reciben una limpieza adecuada, acumulando restos de productos que provocan contaminación cruzada.
- Fallas en la calibración de los equipos: Las máquinas no están configuradas para separar adecuadamente productos diferentes, lo que genera mezclas no deseadas.
- Utensilios compartidos: El uso de cuchillos, bandejas y otros utensilios para múltiples productos sin limpiarlos adecuadamente fomenta la contaminación.
5. Entorno
- Condiciones insalubres en la planta: El entorno de trabajo no cumple con los estándares de limpieza, lo que aumenta las posibilidades de contaminación.
- Contaminación ambiental: Polvo, plagas o productos químicos en la planta pueden entrar en contacto con los alimentos.
- Falta de controles de temperatura: Un ambiente demasiado cálido o frío para ciertos alimentos favorece el crecimiento de bacterias y otros microorganismos.
6. Medición
- Controles ineficaces de calidad: No se realizan suficientes controles para detectar contaminación en las diferentes fases del proceso.
- Herramientas de medición inexactas: Los termómetros o sensores de humedad no están calibrados correctamente, lo que resulta en condiciones de almacenamiento inadecuadas.
- Falta de pruebas microbiológicas: No se realizan pruebas regulares para verificar la presencia de patógenos en los productos.
EJEMPLO 3:
Problema central: Retrasos en la producción de vehículos (Industria automotriz)
1. Método
- Procesos mal definidos: Las instrucciones para la fabricación de vehículos no están claras o no están estandarizadas, lo que genera ineficiencias.
- Cambios frecuentes en los procesos: Modificaciones constantes en las líneas de montaje ralentizan la producción.
- Planificación deficiente: Falta de coordinación entre los departamentos de ingeniería, producción y logística, causando cuellos de botella.
2. Mano de obra
- Falta de capacitación: Los trabajadores no están bien entrenados en los procedimientos de ensamblaje, lo que provoca errores y retrabajos.
- Falta de personal: Hay escasez de mano de obra calificada en momentos clave del proceso de producción.
- Errores humanos: Distracciones, fatiga o descuido de los empleados afectan la velocidad y precisión del ensamblaje.
3. Material
- Escasez de piezas: Los proveedores no entregan los componentes necesarios a tiempo, deteniendo la producción.
- Piezas defectuosas: Se reciben componentes con fallos, lo que obliga a parar la línea de producción para solucionar problemas.
- Variabilidad en los materiales: Los materiales no cumplen con los estándares de calidad o son inconsistentes, lo que provoca que se deban rehacer partes del proceso.
4. Máquina
- Fallas en las máquinas: Los equipos de ensamblaje sufren averías frecuentes, deteniendo la producción.
- Mantenimiento inadecuado: Las máquinas no reciben el mantenimiento adecuado, lo que aumenta el tiempo de inactividad.
- Falta de automatización: Algunas partes del proceso que podrían ser más rápidas con la automatización todavía dependen de mano de obra manual, lo que reduce la velocidad.
5. Entorno
- Condiciones subóptimas en la planta: Espacios desorganizados o poco eficientes para el flujo de trabajo ralentizan el movimiento de materiales y vehículos.
- Problemas logísticos: Retrasos en la entrega de materiales debido a problemas en las cadenas de suministro externas.
- Fallas en la gestión del espacio: El almacenamiento incorrecto de materiales y vehículos en proceso ocupa espacio valioso y ralentiza la producción.
6. Medición
- Falta de indicadores de rendimiento claros: La empresa no mide adecuadamente el rendimiento de cada etapa del proceso, lo que dificulta identificar cuellos de botella.
- Herramientas de medición defectuosas: Los sistemas de monitoreo de producción no están calibrados correctamente, lo que lleva a datos inexactos.
- Poca visibilidad de los retrasos: No hay un sistema efectivo de reporte de los tiempos muertos o paradas en la línea, lo que impide tomar acciones correctivas rápidamente.